Producing sustainable green hydrogen
Hydrogen is produced through various methods, each with distinct economic, technical, safety and environmental considerations. While grey and blue hydrogen are common, the industry is shifting toward green hydrogen for its environmental advantages
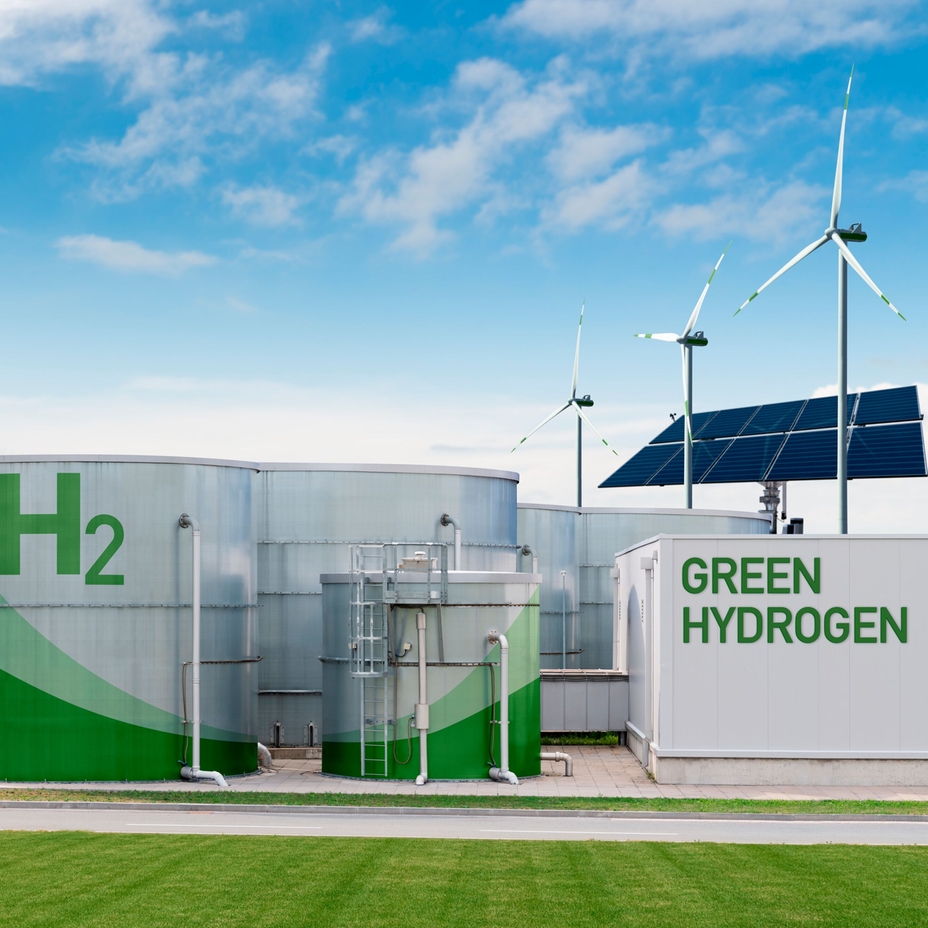
In brief
- Green hydrogen, produced via renewable energy-powered electrolysis of water, is a promising sustainable fuel source. This method offers a zero-carbon alternative to fossil fuels, but faces cost, efficiency and infrastructure challenges.
- Improving electrolysis efficiency is necessary to promote green hydrogen's viability, with several operational and material factors to be considered.
- Scaling green hydrogen production via electrolysis requires addressing high costs, energy losses, the need for specialized infrastructure and insufficient renewable energy supply.
- Despite challenges, green hydrogen has future growth potential, with high demand expected in transportation and heavy industries.
- Advancing green hydrogen's potential requires a collaborative effort, including research to improve efficiency, investments in renewable energy, supportive policies and pioneering companies leading the way.
Powering green hydrogen production
Among hydrogen’s various production methods, green hydrogen is the sustainable standard. Green hydrogen production is powered entirely by renewable energy sources - such as solar, wind and hydroelectric power - making it a carbon-neutral fuel from production to combustion. This sets it apart from other types of hydrogen, including grey hydrogen, which is derived from fossil fuels.

Electrolysis forms the foundation of green hydrogen production, using electricity to split water molecules into their constituent hydrogen and oxygen components. However, capacity, efficiency and cost constraints pose challenges to ramping up production quickly.
Breaking down electrolysis
Electrolysis is a process of electrochemical reactions and ionic transport that takes place within an electrolyzer. Electrolyzers are equipped with two electrodes - an anode and a cathode - separated by an electrolyte. This electrolyte, a liquid solution (for Alkaline) or a solid-state membrane (for PEM), facilitates the passage of ions while restricting the flow of electrons, and it must be carefully chosen based on factors such as ionic conductivity, chemical stability and compatibility with the electrode materials.
When direct current is applied to liquid water within the electrolyzer, an electrical potential difference is established between the anode and the cathode. At the anode, marked by a positive potential, water molecules (H2O) undergo an oxidation reaction, causing a loss of electrons. This results in the formation of oxygen gas (O2), positively charged hydrogen ions (protons, H+), and the release of electrons into the external circuit, which is represented in proton exchange membrane (PEM) electrolyzers as follows:
2 H2O(l) → O2(g) + 4 H+(aq) + 4 e−
The H+ protons migrate through the electrolyte towards the negatively charged cathode, driven by the potential gradient. The cathode promotes a reduction reaction, where the protons readily accept electrons from the external circuit to neutralize their charge and form diatomic hydrogen gas (H2):
2 H+(aq) + 2 e− → H2(g)
The overall electrolytic reaction, a summation of anodic oxidation and cathodic reduction, is represented as:
2 H2O(l) → 2 H2(g) + O2(g)

The efficiency of this process has major implications for the economic viability of green hydrogen production. Several factors impact this efficiency, including:
- Operating temperature, pressure and water purity maintained within the system, which must be accurately measured
- Overpotential required to drive the reactions at a desired rate
- Ohmic losses due to ion transport resistance within the electrolyte
- Mass transport limitations that govern the availability of reactants at the electrode surfaces
Optimizing these variables requires careful material selection, electrode architecture design and measurement and control of all relevant parameters. Among the diverse array of electrolyzer technologies currently available, PEM and alkaline electrolyzers are the most technologically mature and commonly deployed.
PEM electrolyzers, characterized by their use of a solid polymer membrane as the electrolyte, provide several advantages as compared to technologies using a liquid electrolyte, including higher energy efficiency, faster response times to fluctuations in power input and a compact design. These attributes make PEM electrolyzers well-suited for integration with intermittent renewable energy sources like solar and wind power, where power output can vary significantly. They are also typically the choice of laboratories and other operations with an emphasis on high purity end uses.
Alkaline electrolyzers with a liquid electrolyte are not as efficient, but they cost less, have a longer operational lifecycle and accommodate lower water purity than PEM variants. These factors make them attractive in larger green hydrogen production facilities where cost and scale are the primary drivers.
Other technologies in development include high temperature or solid oxide electrolysis and anion exchange membrane. Each have application-dependent competitive dynamics in the hydrogen production technology race.
Barriers to scaled adoption
Despite its appeal as a sustainable fuel throughout the value chain, green hydrogen production presents several challenges.
First, production via electrolysis - particularly with PEM electrolyzers - is more expensive than grey and blue hydrogen production via steam methane reforming or autothermal reforming. Additionally, hydrogen is less energy-dense than natural gas and other fossil fuels and the costs to power processes with hydrogen exceed those powered by fossil fuels per energy unit.
Insights
Green hydrogen - while not yet as low-cost as grey or blue, nor as energy-dense as natural gas - will have an important role as industry pursues net-zero objectives.
Electrolyzer efficiency at the stacks is high - approximately 70 % - with newer technologies like solid oxide electrolyzer cells (SOEC) projected to provide even higher efficiency. However, as with any system, overall plant efficiency is dependent not only on the technology used, but also on the balance of plant for cooling, drying, treating and compressing the hydrogen. Additionally, the supply of renewable energy required to viably scale up electrolysis is lacking, requiring additional investments in infrastructure.
Furthermore, transporting and storing hydrogen is logistically complex due to the need for specialized infrastructure, such as pipelines and storage tanks, designed specifically to handle this highly flammable compound. Current infrastructure is designed primarily for natural gas and unfortunately, it cannot be seamlessly converted due to hydrogen’s unique properties. Hydrogen atoms are the smallest of any element, so diatomic hydrogen gas requires sophisticated pipeline, valve and gasket seals to prevent leakage. It can also weaken many metals as the atoms become lodged in the containment’s internal structure, which lowers the stress threshold and accelerates cracking in unsuitable materials.
The path forward
Addressing these issues requires strategic planning, financial backing from both nation states and private stakeholders and ongoing technological innovation. Despite economic headwinds, electrolyzer deployment is beginning to accelerate. By the end of 2022, global electrolyzer capacity for hydrogen production reached almost 11 GW and capacity is expected to reach 170-365 GW orders of magnitude by 2030.
Additionally, electrolyzer optimization efforts are projected to drive down costs with efficiency in scale, learning and efficiency through the coming decades. This includes targeting higher energy capture from renewables, along with the recapture of intrinsic energy losses during operation. Adjacent technologies, such as hydrogen fuel cells - which are effectively electrolyzers in reverse - will ride the wave of advancement and know-how gained during this transition.
Beyond production, dedicated hydrogen infrastructure is also critical. Hydrogen’s growing viability as an alternative power source is contingent on scaling up the mechanisms required to distribute and convert its energy into useful formats.
Hydrogen demand
The global demand for hydrogen is expected to grow over the next 20 to 30 years, driven by its versatility as an energy carrier and its potential to reduce carbon emissions in hard-to-abate sectors. In particular, the transportation and power generation industries are poised to adopt green hydrogen energy into their portfolios as a clean alternative to fossil fuels.
In the transportation sector, green hydrogen-powered fuel cells offer a promising solution for carbon-neutral commercial transit, such as on trucks, buses and even airplanes. This is especially applicable to long-distance transportation, where battery-powered electric vehicles face range, power generation and weight limitations.
In industry, hydrogen can replace fossil fuels in energy-intensive processes like steel, cement and ammonia production, reducing carbon footprint. Additionally, the power sector is expected to increasingly leverage green hydrogen to store energy from expanding renewable infrastructure, addressing solar and wind power intermittency concerns, without the energy-density and degradation issues of batteries.

Hydrogen is even being blended into the natural gas distribution system to reduce carbon emissions to the atmosphere. Gas-fired stoves, heating systems, clothes dryers and other appliances can burn natural gas with up to a 20% hydrogen blend, which is often limited only by gas infrastructure-defined thresholds. Newer gas turbine and gas engine designs can now blend up to 50% hydrogen into natural gas as a fuel source in power plants, and some smaller turbines up to 100% hydrogen with no natural gas blending required.
Green hydrogen advancement in action
With an intrepid spirit, Spanish multinational utility company Iberdrola is demonstrating its confidence in the hydrogen economy with over 60 green hydrogen projects in development globally. These projects span various sectors - including fertilizer production, green ammonia synthesis and heavy-duty transportation - showcasing the versatility of green hydrogen as a clean energy solution.
Notably, Iberdrola is building Europe's largest green hydrogen plant, which will be primarily used to create ammonia for fertilizer, reducing the ecological impact of this carbon-intensive industry. This landmark project highlights the potential of green hydrogen to decarbonize even the most challenging sectors.
Government initiatives also play a crucial role in accelerating green hydrogen adoption. The U.S. Department of Energy (DOE)'s HyBlend initiative advances green hydrogen by researching how hydrogen can be safely blended with natural gas and transported through existing pipelines. It focuses on pipeline compatibility, material safety and cost reduction, making green hydrogen distribution more affordable and scalable.
Driving green hydrogen viability
Green hydrogen is a cornerstone of the clean energy revolution and it will play an increasingly important role as technology develops. However, realizing its potential requires addressing current production, storage, transportation and infrastructure challenges. This entails further investment in research and development, strategic collaboration among public and private entities and supportive governmental policies.
As renewable energy and hydrogen infrastructure develop, electrolysis efficiency increases and policy evolves, green hydrogen production costs should decrease, addressing another primary barrier to widespread viability. It will require more future-thinking companies and higher-ranking initiatives paving the path for the hydrogen economy with ambitious projects and innovative solutions, reducing global carbon emissions for a more sustainable future.