Nachhaltigkeit fördern mit der Produktion von grünem Ammoniak
Ammoniak ist für Düngemittel und viele Produkte des täglichen Bedarfs unverzichtbar. Für die Netto-Null-Initiativen der Industrie bietet grünes Ammoniak ein großes Potenzial zur CO₂-Reduzierung. Bis zu einer großtechnischen Produktion müssen jedoch noch einige Herausforderungen bewältigt werden.
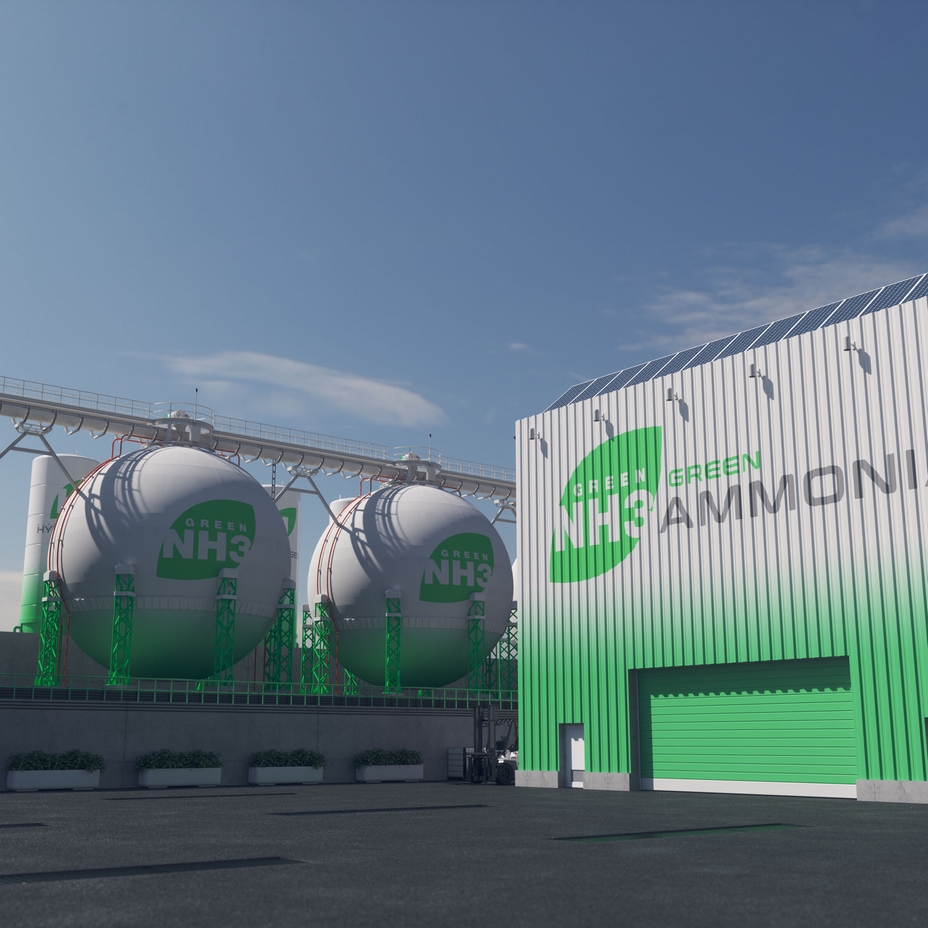
In Kürze
- Ammoniak wird in der Düngemittelproduktion, für Arzneimittel, in der HLK-Technik (Heizung-Lüftung- Klimatisierung) und in verschiedenen anderen Branchen verwendet. Es ist unverzichtbar für die Ernährung der Weltbevölkerung und viele weitere Aspekte moderner Gesellschaften.
- Die Ammoniakproduktion arbeitet hauptsächlich mit dem Haber-Bosch-Verfahren. In der Vergangenheit wurde dafür aus fossilen Brennstoffen gewonnener Wasserstoff verwendet. Das Verfahren trug dadurch erheblich zur Emission von Treibhausgasen bei. Hinzu kommt, das der Prozess üblicherweise mit fossilen Brennstoffen betrieben wurde.
- Der andere wichtige Bestandteil für die Ammoniakproduktion ist Stickstoff, für dessen Herstellung traditionell ebenfalls Energie aus fossilen Brennstoffen benötigt wird.
- Die Nutzung erneuerbarer Energiequellen wie Sonne, Wind und Wasser zur Herstellung von grünem Wasserstoff durch Wasserelektrolyse und für weitere Prozesse eröffnet die Möglichkeit, „grünes“ Ammoniak mit einem kleineren CO₂-Fußabdruck zu produzieren.
- Höhere Investitionskosten zum Aufbau der Infrastruktur für erneuerbare Energien und für Elektrolyseure erschweren derzeit eine flächendeckende Einführung von grünem Ammoniak. Wenn diese Technologien weiter ausgereift sind, werden die Kosten jedoch voraussichtlich sinken und grünes Ammoniak wettbewerbsfähiger machen.
- Ammoniak erfordert strenge Sicherheitsprotokolle, die u. a. Systeme zur Erkennung von Leckagen und Verfahren für einen vorsichtigen Umgang mit Ammoniak festlegen. Fortschrittliche Messtechnik spielt eine entscheidende Rolle bei der Überwachung und Optimierung von Produktionsprozessen, um Effizienz und Sicherheit zu verbessern.
Eine vielseitige Chemikalie für die Industrie
Ammoniak ist eine Verbindung, die nur aus Stickstoff und Wasserstoff besteht und für eine Vielzahl von Anwendungen im modernen Alltagsleben unverzichtbar ist. Als wichtigste Stickstoffquelle für Düngemittel spielt es insbesondere eine entscheidende Rolle in der Lebensmittelproduktion, denn dies ermöglicht ausreichende landwirtschaftliche Erträge, um die wachsende Weltbevölkerung zu ernähren.
Über die Landwirtschaft hinaus wird Ammoniak in großem Umfang in verschiedenen industriellen Prozessanwendungen eingesetzt, darunter:
- Bei der Produktion von Chemikalien, die als Grundstoffe für verschiedene Erzeugnisse wie Kunststoffe, Fasern, Farbstoffe und Sprengstoffe dienen.
- Bei der Herstellung von Arzneimitteln als Ausgangsmaterial für verschiedene pharmazeutische Wirkstoffe sowie zur Steuerung des pH-Werts.
- In der HLK-Technik (Heizung-Lüftung- Klimatisierung) als Kältemittel aufgrund der hervorragenden Wärmeübertragungseigenschaften von Ammoniak.
- In der Lebensmittelindustrie als Zusatz- und Konservierungsstoff.
- Bei der Wasseraufbereitung zur Reinigung in der Wasserversorgung durch Bildung von Chloraminen; diese erleichtern die Desinfektion bei organischen Verunreinigungen.
- In Reinigungsprodukten als wichtiger Bestandteil vieler Haushaltsreiniger aufgrund der entfettenden und desinfizierenden Eigenschaften von Ammoniak.
- In der Textilherstellung beim Veredlungsprozess, um Gewebe zu glätten und ihre Affinität zu Farbstoffen zu verbessern.
Ammoniak ist eine in vielen Branchen unverzichtbare Chemikalie, die herkömmlichen Verfahren der Ammoniakproduktion haben jedoch negative Auswirkungen auf die Umwelt. Deshalb wird nach umweltfreundlicheren Alternativen gesucht.
Konventionelle Ammoniakproduktion nach dem Haber-Bosch-Verfahren
Ammoniak wird hauptsächlich nach dem Haber-Bosch-Verfahren hergestellt. Dabei verbindet sich Stickstoff bei hohen Drücken und Temperaturen in Gegenwart eines Katalysators mit Wasserstoff.

Die einzelnen Schritte sind:
- Stickstoffgewinnung: In einer Luftzerlegungsanlage wird durch einen Verflüssigungs- und Destillationsprozess Stickstoff (N2) aus der Umgebungsluft gewonnen. Alternativ können durch Druckwechseladsorption unter Verwendung spezieller Adsorptionsmittel Stickstoffmoleküle selektiv abgetrennt werden.
- Wasserstoffherstellung: Die Herstellung des benötigten Wasserstoffs (H2) erfolgt üblicherweise durch Dampfreformierung von Methan oder autotherme Reformierung.
- Ammoniaksynthese: Die gereinigten Stickstoff- und Wasserstoffgase werden gemischt und unter hohem Druck (> 200 atm/2.940 psi) und bei hoher Temperatur (> 450 °C/842 °F) über einen Katalysator – üblicherweise Eisen – geleitet. Dabei entstehen elementarer Stickstoff und Wasserstoff, die sich zu Ammoniak (NH3) verbinden.
- Kühlung von Ammoniak, Restwasserstoff und Stickstoff: Die Gase verlassen den Reaktor mit einer Temperatur von über 450 °C (842 °F) und werden von einem Wärmetauscher gekühlt, der gleichzeitig als Abhitzekessel dient. Dadurch entsteht überhitzter Dampf, der anschließend in einer Stromerzeugungsanlage genutzt wird.
- Abtrennung von Ammoniak: Das Gasgemisch wird auf etwa -40 °C (-40 °F) abgekühlt. Dadurch kondensiert Ammoniak und kann aufgrund seines höheren Siedepunkts von nicht reagiertem Stickstoff und Wasserstoff abgetrennt werden. Diese nicht reagierten Gase werden wieder in den Prozess zurückgeführt, um ihre Reaktion abzuschließen.
Der Gesamtprozess wird wie folgt dargestellt: N₂ + 3H₂ ↔ 2NH3
Das Haber-Bosch-Verfahren ist energieintensiv, und bei der Herstellung von braunem, schwarzem und grauem Wasserstoff entstehen erhebliche Mengen an Treibhausgasemissionen. Diese Umweltauswirkungen sind ein gewichtiges Argument, grünen Wasserstoff aus nachhaltigen Quellen zu nutzen und die Stickstoffproduktion mit erneuerbaren Energien zu betreiben.
Produktion von grünem Ammoniak
Die Herstellung des Wasserstoffs für die Ammoniakproduktion ist für etwa 1,8 % der weltweiten CO₂-Emissionen verantwortlich. Dieser Anteil entspricht ungefähr dem gesamten Luftverkehr. Als Antwort auf diese ökologischen Bedenken verfolgt das Konzept des grünen Ammoniaks das Ziel, den CO₂-Fußabdruck der Ammoniakproduktion deutlich zu reduzieren. Dazu sollen die Gase, aus denen es besteht, durch Netto-Null-Prozesse unter Einsatz erneuerbarer Energiequellen gewonnen werden.
Wichtige Erkenntnisse
Die Herstellung des Wasserstoffs für die Ammoniakproduktion ist für etwa 1,8 % der weltweiten CO₂-Emissionen verantwortlich. Dieser Anteil entspricht ungefähr dem gesamten Luftverkehr.
Für die Produktion von grünem Ammoniak werden drei einfache „Zutaten“ benötigt: Luft, Wasser und erneuerbare Energie, um die verschiedenen Prozesse zu betreiben.
Durch kryogene Destillation oder Druckwechseladsorption wird in Luftzerlegungsanlagen Stickstoff aus der Atmosphäre gewonnen. Bei der kryogenen Destillation wird Luft auf extrem niedrige Temperaturen abgekühlt, um die Gase, aus denen sie sich zusammensetzt, anhand ihrer unterschiedlichen Siedepunkte abzutrennen. Eines dieser Gase ist Stickstoff, der für die Ammoniakproduktion benötigt wird. Alternativ können durch Druckwechseladsorption unter Verwendung spezieller Adsorptionsmittel Stickstoffmoleküle selektiv abgetrennt werden.

Die wichtigste Voraussetzung für grünes Ammoniak ist die Verwendung von grünem Wasserstoff. Er wird durch Wasserelektrolyse mit Strom aus erneuerbaren Energien hergestellt und verursacht keine Emissionen. Bei diesem Prozess werden Wassermoleküle in ihre Bestandteile Wasserstoff und Sauerstoff aufgespalten. Das erzeugte Wasserstoffgas wird als Ausgangsmaterial für die Ammoniaksynthese genutzt, und harmloser Sauerstoff wird in die Umgebungsluft abgegeben. Die Elektrolyse findet meistens entweder in alkalischen Elektrolyseuren statt – einer ausgereiften und erprobten Technologie – oder in PEM-Elektrolyseuren mit einer Protonenaustauschmembran, die eine höhere Effizienz und schnellere Reaktionszeiten bieten, allerdings auch höhere Kosten verursachen.
Stickstoff und Wasserstoff werden dann nach dem Haber-Bosch-Verfahren zur Reaktion gebracht, jedoch mit einem kleineren CO₂-Fußabdruck. Alle Prozesse müssen mit erneuerbarer Energie betrieben werden, damit das hergestellte Ammoniak als „grün“ eingestuft werden kann.
Ammoniak kann außerdem durch Ammoniak-Cracking in Wasserstoff und Stickstoff zerlegt werden. Diese Reaktion ist jedoch recht energieintensiv, denn sie erfordert eine Temperatur von 600 °C (1.112 °F) in Gegenwart eines Katalysators. Dieser Prozess wird für einige Anwendungen eingesetzt, für die eigentlich Wasserstoff benötigt wird, weil sich Ammoniak einfacher handhaben und in großen Mengen speichern lässt als reiner Wasserstoff.
Wirtschaftliche Herausforderungen bewältigen
Wie bei vielen CO₂-armen Prozessen ist der Hochlauf der Produktion von grünem Ammoniak mit Herausforderungen verbunden. Sie betreffen hauptsächlich Einschränkungen bei der Infrastruktur und hohe Produktionskosten. Erneuerbare Energien verzeichnen zwar ein schnelles Wachstum, bei Netzintegration und Stromspeicherung müssen sie aber erst noch an das Niveau konventioneller Systeme heranreichen, damit sie den Bedarf für Industrie und Konsumgüter decken können. Auch bei Elektrolyseuren für die Herstellung von grünem Wasserstoff sind für den Hochlauf dieser Technologie noch gewaltige Investitionen erforderlich.
Mit der zunehmenden Ausgereiftheit nachhaltiger Technologien und der Realisierung von Größenvorteilen wird die Produktion von grünem Ammoniak jedoch immer wettbewerbsfähiger werden. Die Kosten für erneuerbare Energien sind in den letzten Jahren gesunken, und dieser Trend wird sich voraussichtlich fortsetzen. Dies erhöht die wirtschaftliche Realisierbarkeit von grünem Wasserstoff und Stickstoff.
Es gibt auch Pilotprojekte für Ammoniak als CO₂-freien Energieträger, und in einigen Anwendungen wird sogar eine direkte Verbrennung erprobt,
um die Einschränkungen bei Sonne- und Windenergie zu überwinden, die durch die intermittierenden Erzeugung bedingt sind. Aufgrund der hohen Energiedichte von Ammoniak wird auch an seiner Nutzung als Kraftstoff für Schifffahrt und Langstreckenverkehr geforscht, beides traditionell Anwendungen mit hohem CO₂-Ausstoß.
Sicherheitsaspekte und fortschrittliche Messtechnik
Trotz des hohen wirtschaftlichen Nutzens von Ammoniak darf nicht vergessen werden, dass es eine gefährliche Chemikalie ist, die mit Vorsicht gehandhabt werden muss. Bereits eine Ammoniakkonzentration in Luft von nur 0,5 % kann beim Einatmen für den Menschen tödlich sein. Ammoniak ist stark ätzend und giftig. Dies erfordert strenge Sicherheitsprotokolle bei Herstellung, Transport und Verwendung.
Neben der standardmäßigen persönlichen Schutzausrüstung und gründlichen Mitarbeiterschulungen sind Systeme zur Erkennung von Leckagen ein wichtiges Hilfsmittel der Gefahrenminderung, falls es zum Versagen einer äußeren Umschließung kommen sollte. Diese Systeme bestehen aus elektrochemischen Gasdetektoren, Druckmessumformern und weiterer fortschrittlicher Sicherheitsinstrumentierung mit ihren zugehörigen Komponenten.
In Luftzerlegungsanlagen, mit denen Stickstoff aus der Luft für die Ammoniakproduktion gewonnen wird, kommen außerdem Messgeräte wie TDLAS-Analysatoren für Reinheitsanalysen sowie Drucksensoren für die Prozesssteuerung zum Einsatz. Beim Prozess der Wasserelektrolyse überwachen Leitfähigkeitssensoren die Qualität des Elektrolyten und gewährleisten damit eine optimale Leistung und Langlebigkeit des Elektrolyseurs. Durchflussmesser sind eine wichtige Komponente für die Regulierung der Wasserstoff- und Sauerstoffproduktion.
Im Ammoniaksynthesekreislauf werden viele verschiedene Messgeräte verwendet, u. a. Temperatursensoren, Druckmessumformer und Gasanalysatoren, um die Reaktionsbedingungen zu optimieren und eine hohe Produktqualität sicherzustellen. Diese Messgeräte liefern kontinuierlich Daten, die sowohl für die Echtzeitsteuerung als auch für spätere Auswertungen genutzt werden. Dies ermöglicht dem Personal, den Prozess zu optimieren und die Effizienz zu maximieren, gleichzeitig jedoch sichere Betriebsbedingungen aufrechtzuerhalten.
Bei der Ammoniakzersetzung werden Durchflussmessgeräte für eine präzise Gaszufuhr und optimale Reaktionsgeschwindigkeiten benötigt. Thermoelemente sorgen für eine genaue Temperaturmessung, und Gasanalysatoren überwachen die Zusammensetzung des Wasserstoffstroms, um dessen Reinheit zu gewährleisten.
Ausblick in eine grüne Zukunft
Ammoniak ist in zahlreichen industriellen Prozessen, die Verbraucher oft für selbstverständlich halten, von unschätzbarem Wert. Trotzdem sind für eine flächendeckende Einführung von grünem Ammoniak noch erhebliche Hindernisse zu überwinden. Die Infrastruktur für erneuerbare Energien und Elektrolyse ist nach wie vor begrenzt und die Investitionskosten sind hoch. Da Ammoniak ein Gefahrstoff ist, erfordert die Gewährleistung der Sicherheit bei Transport und Lagerung große Sorgfalt, hierfür gibt es jedoch bewährte zugelassene Verfahren.
Der Hauptvorteil von grünem Ammoniak besteht darin, dass er die Ammoniakproduktion von der Abhängigkeit von fossilen Brennstoffen entkoppelt und dadurch Treibhausgasemissionen reduziert. Aus diesem Grund sind Regierungen ebenso wie die Industrie auf grünes Ammoniak aufmerksam geworden, sodass diese Akteure das Produkt inzwischen in ihre Strategien für Nachhaltigkeitspläne aufgenommen haben. Ammoniak zeigt einen Weg auf, wie der CO₂-Fußabdruck in der Düngemittelindustrie und in unzähligen weiteren Branchen mit intensiver Ammoniaknutzung reduziert werden kann.
Weitere Anstrengungen bei Forschung und Entwicklung sowie kontinuierliche Innovationen bei Produktions- und Nutzungstechnologien sind grundlegende Voraussetzungen für eine flächendeckende Einführung von grünem Ammoniak. Es ist ein wichtiger Baustein, damit bis Mitte des Jahrhunderts die weltweit angestrebten Netto-Null-Ziele erreicht werden können.